Uncategorized
Optimizing Excellent Operations Through Quality Management And Control
The business sector is growing day by day, facing more competition in the market. Business needs quality management and control of their operations to survive efficiently with the cutting-edge competition. The implementation of highly strong strategies for quality can result in favor of excellent operations. By implementing these strategies the business can not only foster operational performance but also improve the rate of customer satisfaction with continuous improvement and innovation.
An understanding of the role, strategies, and process is essential for the betterment of operational functions. Effective implementation of these attributes can increase business standards and ethical practices. These aspects of quality management and control are further discussed in this article.
The role of Quality Management and Control in operations
Quality management helps businesses to achieve greater consistency in production activities and processes. It increases efficiency, reduces waste, and utilizes time and resources. Their main focus is to continuously improve business operation management. Whereas, quality control is an ongoing process in operations. Business needs to safeguard their reputations, prevent products from being unreliable, and increase trust on the side of consumers. So, the purpose of testing is to determine if any corrective actions are required in the manufacturing process.
Thus quality management and control are important for business as they provide a framework for constant quality improvement. This gives assurance to companies for building and launching the best possible product and service.
Learning quality management and control skills is vital for students who have opted for operations management studies. Mastering these skills enables students to design and implement strategies that enhance product and service quality and reduce operational costs. In total, these are a great start for your career growth. To catalase their learning, students search for operation management assignment help services to seek guidance from experts and improve their knowledge efficiently.
Difference between Quality Management and Quality Control
Quality management and quality control both are important for operations but they serve different purposes. Quality management is a comprehensive approach that focuses on a long-term quality foundation within the organization. It includes planning, designing, and implementing quality assurance processes to meet production standards consistently.
On the other hand, quality control focuses on operational techniques and activities used for fulfilling quality requirements. It involves inspection, testing, and verification of products and services to identify defects and ensure they meet quality standards. It is more about identifying detects and correcting them whereas, quality management is about prevention and planning for quality in every step of production.
Top 5 Quality Management Strategies
Quality management is the process of overseeing all the tasks and activities that must be accomplished to achieve the desired excellence. To achieve that there are strategies to be implemented for consistent quality management. Some of the commonly used strategies are given below:
- Register Quality
Quality registers are usually been created at the initial stage of any project. So, that all the activities are registered properly and they all can serve as a reference for clarification. Quality registers help the business to keep a record of all the results of quality control operations.
- Continuous improvement
Continuous improvement is an ongoing process that is used to reduce waste, time, and effort during the production process. Businesses need to be actively involved in continuous improvement as it directly reflects on the quality management of the company. It helps the organization abilities to embrace new opportunities.
- Periodic internal audits
The audit results provide managers with improvement suggestions regarding current processes and operations. Eventually, it will boost the quality of service and products. Internal audits are generally done to take action on compliance with regulations and laws.
- Process approached
Every operation needs a correct approach to the process. Because producing the right output requires the use of the right input. This process approach strategy emphasizes achieving effectiveness and efficiency in the production process. If the process approached is managed successfully then quality is assured.
- Customer Focused
The strategy is to focus on satisfying customers and maintaining good relationships with them. Businesses should follow up on customer service situations, which will help them define areas for improvement. Through this strategy, the operation department can know their mistakes and they can continuously work on improving the manufacturing process.
Process for Quality Control
The main aim of quality control is to ensure that every time the process is performed with the same information, skills, methods, and control used and applied in the same manner. To carry this operation consistently there are some processes to be followed which are :
- Establish control
The set of controls under which every product and service should match with all the aspects of quality control. These controls should be properly listed and documented so, there is no issue in understanding and implementing them. Before production begins both the development and quality departments should aligned with controls.
- Test and check product standards
The checking of products and services is very important even if they are produced as per the defined controls. Testing is the process of checking the product as a whole and also as modules to cover as many scenarios as possible.
- Analyze variances
Analyzing variances or differences within the set control and quality standards. If there are any variances detected then they should be well analyzed and documented. So, to make sure the right numbers are there and the extent issues can be assessed.
- Check and define limits
There should be proper checking to see if the differences are within the statistical data. This is considered to be a tolerance level that can be presented as 10% to 15%. If the difference is within this limit then the product doesn’t need any action.
- Corrective decisions
If the difference is a lot then corrective action and correction are need to be taken. Either it is a rejection of the whole batch or sending them back for improvement in the overall quality. The entire process is repeated to make sure no defective product reaches customers.
- Feedback
Quality control is an ongoing process that keeps improving in every development cycle. So, the quality of data and feedback should all be properly analyzed for future aspects. Quality control is linked to statistical procedures as they lend quantitative authenticity to statistical control of the operations.
Conclusion
Quality management and quality control play crucial roles in ensuring the efficiency and effectiveness of operations. Quality management encompasses the overall process of planning, controlling, and improving quality. There are many quality management strategies used to be successful in the process. Quality control focuses on the operational techniques and activities used to achieve quality standards. Quality management and control are intrinsically linked with the operation as they directly impact production performance.
Uncategorized
How to Sell Inherited House Columbia SC Without the Stress
If you’ve recently inherited a property in Columbia, South Carolina, you may be wondering what to do next. Whether you’re dealing with a single-family home, a townhouse, or even a multi-unit property, the big question is—how do you sell inherited house Columbia SC without all the hassle?
You’re not alone. Many people inherit homes and are unsure about their legal and financial responsibilities. The good news is, there are easy and legal ways to sell inherited house Columbia SC, even if it’s still in probate or needs some repairs. In this blog, we’ll break down the steps, answer common questions, and guide you through the process with simple and clear information.
Understanding the Process of Selling an Inherited House
Before jumping into selling the house, it’s important to understand a few key things. When someone passes away and leaves you a house, that property may go through probate—a legal process used to validate the will and distribute the estate.
This brings us to an important question many people have:
Can I sell my house in probate in Columbia?
Yes, in most cases, you can. But it depends on your role in the estate, if the will names you as the executor, and whether the court gives you permission to sell the property. Probate sales are common in Columbia and can be managed easily with professional help.
Step-by-Step Guide to Sell Inherited House Columbia SC
Step 1: Confirm Ownership and Legal Standing
The first step is to confirm that you have legal rights to sell the property. If the house is going through probate, consult with a probate attorney or legal expert in South Carolina to guide you through the paperwork.
If probate has already been completed and the house is now legally in your name, you can proceed with the sale as you would with any other property.
Step 2: Evaluate the Condition of the House
Many inherited homes are older and may not be in the best condition. If you’re asking yourself, “how to sell my house Columbia SC when it needs repairs?”—don’t worry. You have options:
- Sell As-Is: Companies like RedHead Home Properties specialize in buying homes in their current condition. That means no repairs, no cleaning, and no updates required.
- Fix and Sell: If you have time and money, you can renovate the house to increase its market value. But this often leads to higher costs and delays.
Step 3: Decide If You Want to Sell with an Agent or Sell Directly
When you sell inherited house Columbia SC, you can either list it on the market with a real estate agent or sell directly to a cash buyer. Here’s a quick comparison:
Selling with Agent | Selling to RedHead Home Properties |
May take weeks or months | Can close in as little as 7 days |
Requires repairs and showings | No repairs or showings needed |
Agent commissions apply | No commissions or fees |
Uncertain timeline | Guaranteed offer and fast closing |
Many people who need to sell my estate Columbia SC quickly prefer to work with direct home buyers to avoid delays and uncertainty.
Step 4: Understand the Tax Implications
When you inherit a house, you may be responsible for property taxes, capital gains taxes, or other estate-related costs. However, South Carolina has a “step-up” in basis rule. This means the property value resets to the market value at the time of the previous owner’s death, which often reduces your capital gains if you sell shortly after inheriting.
It’s best to talk to a local tax advisor to fully understand what you may owe.
Step 5: Get a Fair Cash Offer
If you want to avoid listing your home, paying agent fees, or dealing with buyer inspections, request a cash offer from a local real estate investor like RedHead Home Properties.
Here’s what you can expect:
- No repairs needed
- No commissions or closing costs
- Flexible closing timeline
- Guaranteed offer—no surprises
Common Reasons to Sell an Inherited House in Columbia
People choose to sell inherited house Columbia SC for many reasons, such as:
- You live out of state and don’t want to manage the property.
- The house needs expensive repairs or updates.
- You’ve inherited the home along with other siblings and want to split the cash value.
- You want to avoid the responsibilities of being a landlord.
- You’re facing property taxes or legal fees tied to the home.
No matter your reason, selling doesn’t have to be complicated or stressful.
Why Choose RedHead Home Properties?
RedHead Home Properties is a trusted local company that helps homeowners just like you sell my estate Columbia SC quickly and fairly. We understand how emotional and complicated it can be to part with a family home. That’s why we:
- Offer no-obligation cash offers
- Handle all the paperwork and legal details
- Pay closing costs, so you don’t have to
- Provide support every step of the way
Whether you’re still navigating probate or just inherited the house and want to move on, we’re here to make the process smooth and stress-free.
Final Thoughts
Inheriting a house can be both a gift and a challenge. If you’re wondering how to sell inherited house Columbia SC, remember you have options. Whether it’s in probate, outdated, or simply no longer needed, you can sell it fast, fairly, and without the usual headaches of listing it on the market.
You don’t need to handle this alone. If you’re ready to move forward, reach out to RedHead Home Properties today. We’ll help you understand your options and give you a no-hassle cash offer—so you can focus on what matters most.
Uncategorized
Psychic Website Design Services: Build a Spiritually Aligned, SEO-Optimized Website
In the digital era, your website is the face of your psychic brand. Whether you offer tarot readings, energy healing, astrology, or spiritual guidance, your online presence must reflect your unique energy and attract the right clients. At Vega Moon Technologies, we specialize in Psychic Website Design that combines creativity, functionality, and SEO excellence to elevate your spiritual business.
Why a Well-Designed Psychic Website Is Essential
A professionally crafted psychic website not only showcases your services but also builds trust, drives traffic, and boosts bookings. Here is why it matters:
- First Impressions Count: Visitors form opinions in seconds. Make sure your website reflects your authenticity and professionalism.
- Built-In SEO Benefits: Our sites are structured for search engine visibility using E-E-A-T SEO guidelines.
- User-Focused Design: Smooth navigation, fast load times, and intuitive interfaces enhance the overall user experience.
What Our Psychic Website Design Services Include
Personalized Design for Every Psychic Brand
We ensure your branding—colors, fonts, icons, and images—reflects your offerings, whether it is clairvoyance, numerology, or energy healing. Every detail is customized to match your aura and style.
Smooth and Simple Navigation
Visitors should easily find your services, blog, contact form, and booking page. We structure your psychic web to guide users with clarity and simplicity.
Mobile-Responsive Websites
More than half of your audience is browsing on smartphones. Our psychic website design ensures responsiveness across all screen sizes for a consistent experience.
Online Booking and Secure Payment Integration
Make it effortless for clients to schedule sessions and pay securely. This builds trust and increases conversions.
Built-In SEO for Your Psychic Web
Our web design does not just look good—it is built to rank. We apply the latest SEO strategies that align with E-E-A-T standards:
- Keyword Optimization: Strategic use of terms like Psychic Website Design, Psychic Website, and Psychic Web helps boost your visibility without keyword stuffing.
- Metadata Optimization: Titles, descriptions, and alt tags are all customized to improve search engine ranking.
- Content Structure: We use proper heading hierarchies (H1, H2, H3) and internal linking to guide both users and search engines.
Key Features of a High-Converting Psychic Website
- Visually stunning layouts
- Easy-to-use navigation
- Fast page speed
- Blog setup for ongoing SEO
- SSL certification for secure browsing
- Accessible design for all audiences
Why Choose Vega Moon Technologies
Choosing a specialized agency for your psychic website design ensures your online presence aligns with your spiritual mission. Here is why Vega Moon Technologies is the perfect partner:
Niche Understanding
We understand the spiritual and psychic niche, which allows us to design websites that speak directly to your ideal audience.
SEO-Driven Results
We combine attractive design with search engine optimization so your psychic web can be found by the people searching for your services.
Ethical SEO Practices
We follow white-hat SEO strategies. All keywords, like Psychic Website and Psychic Website Design, are naturally embedded without overuse, ensuring compliance with search engine algorithms.
Ongoing Support and Growth
Our relationship does not end with the launch. We offer ongoing maintenance, updates, and SEO enhancements to keep your psychic website growing with your business.
How We Align with E-E-A-T SEO
- Experience: We design sites that reflect your real-world services and spiritual experience.
- Expertise: Our team is skilled in both web development and SEO for niche industries.
- Authoritativeness: By structuring content and linking properly, your site earns domain authority over time.
- Trustworthiness: We implement secure, compliant features that protect user data and create a credible online image.
Ready to Build or Refresh Your Psychic Website
If you are launching a new spiritual business or want to refresh your current site, Vega Moon Technologies offers custom, SEO-optimized psychic website design that attracts the right audience and turns visits into bookings.
Contact Us to Begin Your Psychic Website Design Journey
Let Vega Moon Technologies create a psychic web that is aligned with your energy, optimized for SEO, and designed to grow with you. Whether you are a solo practitioner or a team of spiritual healers, your next digital chapter begins here.
At Vega Moon Technologies, we specialize in psychic website design that resonates with your spiritual brand. Our expert team blends mystic aesthetics with cutting-edge tech to create a powerful digital space where your light shines brightest. If you’re ready to grow your spiritual practice and connect with seekers worldwide, read on to discover why a custom psychic web design is your next divine move.
At Vega Moon Technologies, we’re more than just a tech company—we’re your digital growth partners. Visit Vega Moon Technologies to schedule your free consultation today.
Uncategorized
Zero Liquid Discharge zero liquid discharge and wastewater treatment systems Explained
Wastewater Treatment Explained
Wastewater and water treatment are essential for managing environmental impact and meeting industrial regulations. These processes remove contaminants from water used in homes, factories, and commercial setups. As fresh water becomes increasingly scarce, wastewater treatment provides a sustainable solution to recycle and reuse water for various applications.
Concept and Principles of Zero Discharge System
The Zero Liquid Discharge (ZLD) system is a cutting-edge wastewater and water treatment method designed to eliminate liquid waste entirely. Its core principle involves purifying wastewater to recover clean water while converting remaining impurities into solid waste. This advanced approach not only minimizes environmental risks but also ensures that no untreated effluent enters natural water bodies.
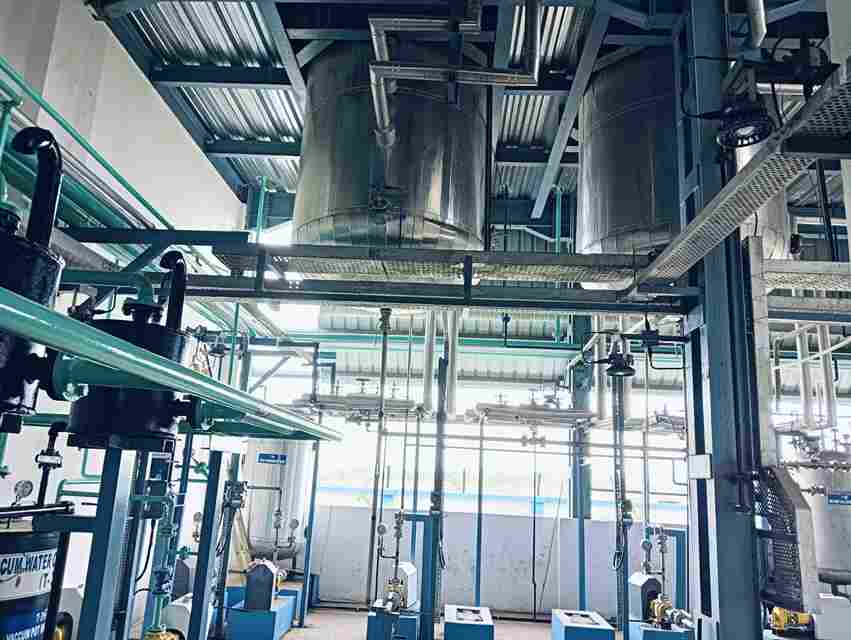
Components of Zero Discharge System
A ZLD system includes several key components working in harmony:
- Pretreatment Unit: Removes large particles and oil.
- Evaporators: Concentrate brine from wastewater.
- Crystallizers: Convert brine into solid waste.
- Filtration Units: Eliminate fine particulates.
- RO Systems: Perform membrane-based water purification. These units ensure high recovery rates and near-complete pollutant removal.
Operational Process of Zero Discharge System
The wastewater and water treatment cycle in a ZLD system begins with screening and filtration. It is followed by reverse osmosis (RO), which removes most dissolved salts. The concentrate from RO is treated in evaporators. Finally, crystallizers turn the remaining brine into manageable solids. Recovered water is returned to the process line, achieving near-total water reuse.
Benefits of Zero Discharge System
ZLD offers an environmentally responsible solution to industrial wastewater and water treatment. The system not only recycles water but also ensures zero contamination. Industries can adhere to stringent discharge regulations while preserving natural water resources.
Environmental Benefits
ZLD plays a critical role in minimizing water pollution. It prevents the discharge of toxic wastewater into rivers and oceans. This system reduces groundwater contamination and supports sustainable development goals. By reducing environmental footprints, ZLD systems protect ecosystems and enhance biodiversity.
Economic Benefits
Although the initial setup for a ZLD system might be high, long-term gains are substantial. It reduces water procurement costs by recycling internal wastewater. Also, the recovery of valuable byproducts from waste streams adds economic value. Reduced environmental penalties and compliance with government regulations offer additional savings.
Challenges and Solutions in Implementing Zero Discharge System
Technical Challenges Implementing ZLD requires advanced technologies and trained personnel. System complexity and high energy consumption pose technical hurdles. Integrating innovative solutions like MEGA RALEX® ED(R)-IF electrodialysis can improve efficiency and reliability.
Economic Challenges Upfront capital investment is a common concern. However, modular systems and phased implementation can reduce initial financial burdens. Government incentives and environmental subsidies further ease adoption.
Regulatory Challenges Different regions have varying wastewater discharge regulations. Companies must remain updated with evolving standards. Partnering with experienced providers ensures systems comply with legal frameworks.
Applications of Zero Discharge System
ZLD systems find use across multiple sectors that demand responsible wastewater and water treatment. From large industries to city municipalities, the demand for clean water makes ZLD a vital component.
Industrial Applications
Industries like chemicals, textiles, power generation, pharmaceuticals, and mining extensively use ZLD. These sectors generate large volumes of wastewater with high pollutant loads. ZLD not only manages the waste but also helps recover usable water.
Municipal Applications
Urban wastewater treatment plants are turning toward ZLD to meet stringent regulations. Cities facing water shortages benefit immensely from ZLD, as it recycles municipal sewage for non-potable applications like gardening and flushing.
What is Zero Liquid Discharge?
Zero Liquid Discharge (ZLD) is an advanced approach to wastewater and water treatment that ensures no liquid effluent leaves a facility. It’s a closed-loop system that emphasizes water reuse and solid waste minimization.
ZLD – The Advanced Water Treatment Process
ZLD combines physical, chemical, and thermal processes to achieve complete wastewater purification. Innovations in membrane technology and thermal evaporation enhance system effectiveness while reducing operational costs.
Zero Liquid Discharge System
A well-integrated ZLD system not only meets environmental compliance but also serves as a long-term investment. With continuous R&D, modern ZLD systems are more energy-efficient, compact, and easier to operate.
Benefits of ZLD Plant
- Complete water recovery
- Reduced discharge costs
- Enhanced sustainability image
- Resource recovery (salts and metals)
- Improved compliance with pollution control norms
ZLD System by MEGA
Goldfinch utilizes MEGA’s RALEX® ED(R)-IF – a globally renowned electrodialysis system. This technology enhances the performance of ZLD systems, offering unmatched efficiency in brine treatment. MEGA’s solutions support industrial use across power plants, petrochemicals, and more.
Advantages of MEGA Electrodialysis in ZLD Processes
- High recovery rates
- Low operational cost
- Compact footprint
- Durable membranes
- Minimal maintenance
Advantages of RO Brine Treatment by MEGA ZLD System
Reverse osmosis often creates concentrated brine. MEGA’s advanced technology converts this brine into reusable water and solids. It helps achieve true zero discharge with reduced energy consumption.
Our ZLD Projects
Goldfinch has successfully implemented ZLD systems across various industrial sites in India. From chemical plants to textile mills, our compact solutions deliver high efficiency and low operational costs. Our experience and partnership with MEGA technologies make us a trusted leader.
Explore Our Goldfinch Solutions
Goldfinch Evaporators has been a pioneer in Zero Discharge Systems in India for over four decades. We specialize in innovative vapor recompression technology and compact ZLD systems suitable for diverse industries. Our robust design ensures long-lasting performance with minimal environmental impact.
Looking for Zero Discharge System?
If your facility is aiming for complete wastewater reuse, Goldfinch’s ZLD systems are your best option. Our solutions are tailored to meet unique industrial demands and regulatory needs.
Our Compact Range of Zero Discharge System
Designed for efficiency and ease of integration, our compact ZLD range offers:
- Small footprint
- Low maintenance
- Scalable capacity
- Quick ROI
Conclusion
Zero Liquid Discharge systems are redefining the way industries handle wastewater and water treatment. By ensuring no effluent discharge and promoting water reuse, ZLD supports both environmental and business sustainability. Goldfinch, in collaboration with MEGA, brings the best of global technology and local expertise to serve your ZLD needs.
Whether you’re planning a new facility or upgrading an existing one, explore our Goldfinch ZLD solutions for a cleaner, sustainable future.
- Business & Services4 days ago
Crafting a Winning Operations Strategy for Sustainable Business Growth
- Education3 days ago
What to Do If Your Child Is Behind on 11 Plus Prep for Grammar Schools in High Wycombe?
- Travel & Event4 days ago
Etihad Wheelchair Assistance – Accessible Air Travel Support
- Uncategorized4 days ago
Car Parking Multiplayer: A Realistic Open World Driving Game for Racing and Tuning Fans
- Blog4 days ago
Highmoon Office Furniture: Dubai’s Go-To for Stylish Workspaces
- Blog4 days ago
HVAC Maintenance Tips for First-Time Homeowners
- Uncategorized3 days ago
Industrial Rugged Tablets: The Future of Industrial Automation in India
- Sports5 days ago
QiuQiu99 Situs Resmi DominoQQ Pkv Games Login Terpercaya